A visit to Tata Motors’ CVBU and PVBU plant in Pune
Tata Motors invited a bunch of journos for a tour of its manufacturing facility located in Pimpri –Chinchwad to make us acquainted with their NVH labs, climate control and crash test facilities
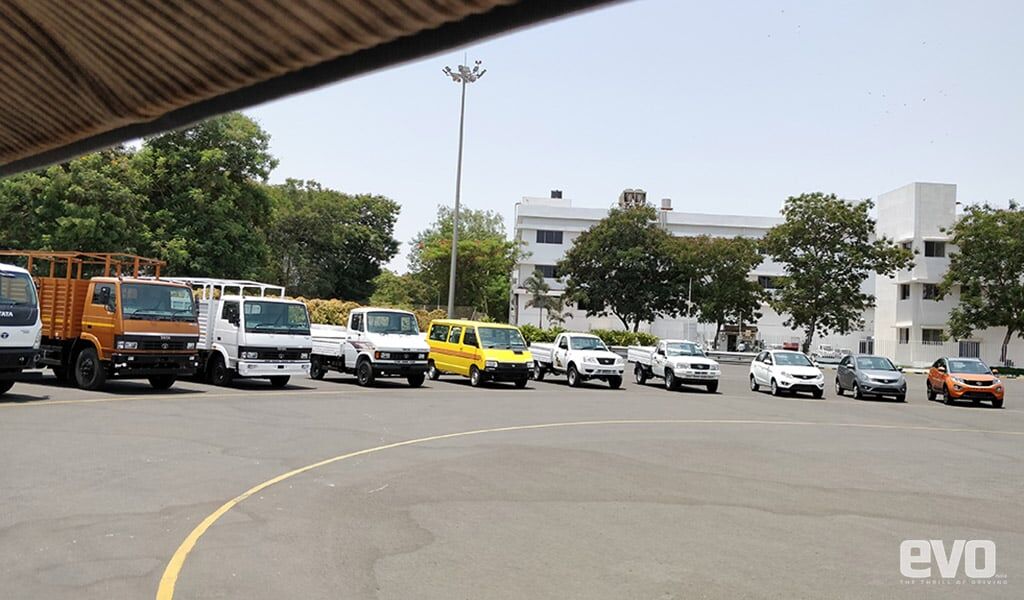
The 1000 acre Tata Motors plant in Pimpri-Chinchwad
Tata Motors has arguably one of the biggest manufacturing setup in the entire nation with its CV and PV units put together. ‘Sumant Moolgaonkar was one of the prime architects of Telco (now Tata Motors) and the Sumo was named after him, not a Japanese wrestler’, said our guide D V Tilak. After the media briefing, we were taken to a tour of its commercial vehicle plant where different components of the trucks like gearbox, sheet metal, cabin, axles and chassis were all being assembled together. There is an in-house training facility too, where all the new recruits are given classroom knowledge before they are sent to the shop floor for their training/job.
The commercial vehicle section
As we were taken to the commercial vehicle block, on display was the chassis of the first truck made in collaboration with Mercedes-Benz, from 1954-1977. Yes, Tata and Mercedes-Benz had a joint venture back then to make commercial vehicles. The engine of that vehicle is cut half which is now used as a demo vehicle to show the working of an IC engine for the trainees. A bespoke 1926 Rolls-Royce Silver Ghost is also put on display to give a glimpse of what the 1920s looked like.
A quick look at the stats
Apparently, around 800 commercial vehicles (trucks and busses) and 1200 cars are assembled everyday at the Chinchwad facility. It takes two hours for assembling trucks and the company uses automated robots (made in Germany/Japan) to weld and assemble. Manual welding is used in areas where the robots cannot reach; e.g. welding of the suspension mount bracket. The sheet metal scrap generated whilst making the dies for the different components like windows, doors, roofs of the commercial and passenger vehicles are stored two stories below the ground and is later subjected to foundry, where they are melted and reused by the company. A car is made from scratch in five and half hours. 50 Tata Hexas are assembled every day at the plant. Tata also has the largest tool room in Asia. Apart from making dies for its own vehicles, it also makes and supplies dies to other OEMs including Renault, Toyota, Honda and TVS.
The evolution of Indica to H5X and more
One of the first indigenously built cars by any Indian company, the Tata Indica was first unveiled in 1998. Tata Motors recently pulled the plug on the Indica, saying it had done its job well and it was time to move on. Today, you will find the company’s latest projects like the Q5, H5X and the 45X are driven around the facility, fully camouflaged. During the media interaction, we also got to know from Tata Motors’ president and chief technology officer Rajendra Patekar that the H5X and the 45X will be made at the Pune facility. The ERC (Engineering Research Centre) is also a part of the facility where all the concept cars are assembled to showcase at various motor shows around the world.
The anechoic chamber
The company’s NVH facility was inaugurated in 1996 and is the Asia’s first anechoic chamber installed by an automaker. Upon entering the anechoic (no-echo) chamber, the doors were sealed and there was pin-drop silence. The walls and ceiling comprise over 19000 wedges that are 1.2m long, and are arranged so as to form a ‘T’ shape. The wedges are made of glass wool on the inside and jute packing on the outside, which act as noise absorbing materials. Now imagine hundreds of ‘T’ wedges staring at you from the top and the walls with fairly dim lighting. It was quite a scene. The floor we were standing on had 56 rubber mounts beneath it so that no vibrations creep up into the NVH room due to passing vehicles or other disturbances. The NVH room uses sensors everywhere to detect and pinpoint the location low amplitude noises which the engineers at Tata call it as ‘irritating noises’ that come from the car during the test. Proper ventilation is provided to breathe in clean air while also drawing the exhaust fumes of the vehicle outside. The NVH facility is used to test all the vehicles – CV and PV.
The climate control chamber
Tata Motors says that it is India’s first climate test facility. The climate test facility of Tata Motors has two chambers – a hot chamber and a hot and cold chamber. The maximum temperature of the chamber is 55°C for simulating hot conditions, a -40°C is the lowest temperature for simulating cold conditions. A Tata Ace was subjected to the hot chamber when we were at the facility. The duration of the test is subject to variation and changes from vehicle to vehicle. Useful information like the ageing of the rubber and plastic components the functioning of all sensors and electronics and their durability at extreme temperatures can be known. Cold chamber test is used to gauge the behavior of the engine coolant, engine performance, the condition of the plastic and rubber components, corrosion behavior among other parameters.
The crash test facility
The crash test facility is as well the first for an Indian car maker that is used to test PV, CV and defense vehicles. The crash test facility is equipped with conducting frontal, offset, pole, and side-pole impact tests for passenger vehicles. For busses, static rollover test is conducted to check the strength of the bus top superstructure. A pendulum test (oscillation of the truck’s cabin during impact) is also conducted for trucks to check the damages of the cabin and the safety of the driver and occupants. Giving all the readings for the crash tests are the test dummies that are used for various tests like frontal crash, side crash etc. The cost of one dummy is north of Rs 1.2 crore. And they have a family of dummies for testing. The crash test facility uses high speed motion capture camera and non-flickering lights. There is also a transparent glass panel that houses another high speed camera on the floor at the very end of the impact area to capture the damages borne by the underbody during the crash.
More tests
The company also conducts a series of tests which they call ‘misuse-abuse conditions’. These include driving a car at high speeds bang into a pothole to see if the airbags are deployed, which shouldn’t in this condition. Tata calls this as ‘ditch drop’. A ‘deer hit’ (they don’t use a live deer for this) and ‘kerb hit’ test too are done so that the airbag does not accidentally deploy when it shouldn’t. These tests help the crash test engineers to check the performance of the airbag sensors and other components of the car. A ‘mine blast’ test is conducted on defense vehicles – basically blowing up the vehicle – to simulate the impact of a mine blast on the vehicle as well as the occupants inside the vehicle.
At the end of our plant tour, we were briefed about Tata’s new ‘Impact 2.0’ design language, the ‘Alpha architecture’ for cars and sedans, etc. by the CTO of Tata Motors, Rajendra Patekar. As told to us, a lot of investment is made by the company on the BS VI norms. The company believes that electric vehicles will take time to hit the roads due to the lack of a charging infrastructure.