So you want more REVolutions?: The science of revs
Ducati’s new Panigale V4R makes massive power, thanks to a sky-high rev limit. How does it do it, and why are revs so important for power? Let’s find out
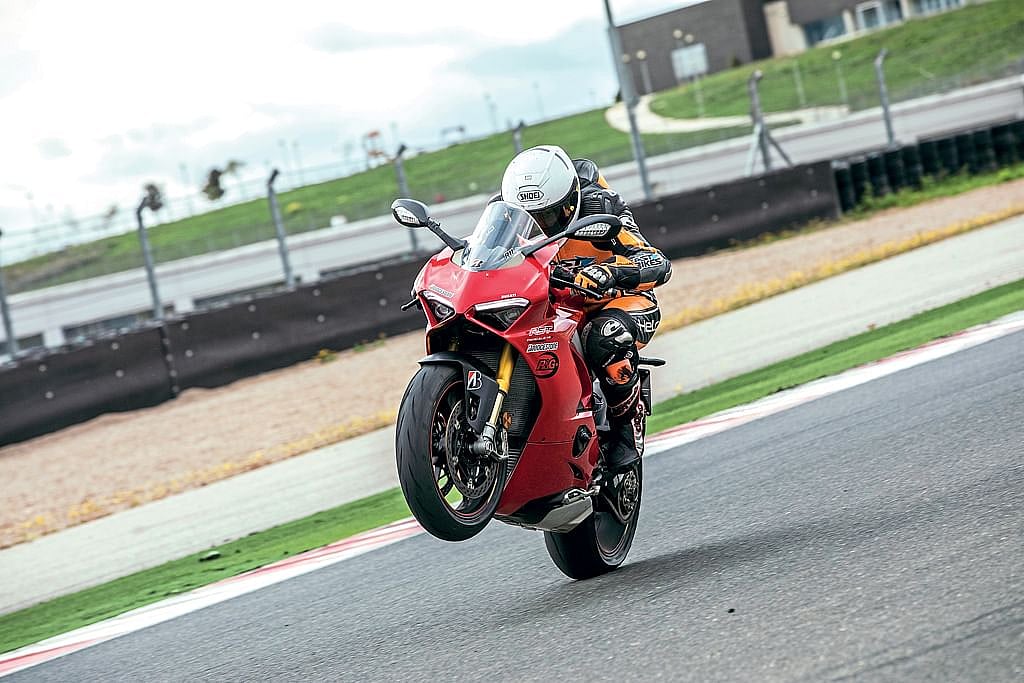
I freely confess that I’m a bit jaded and cynical these days. It takes a lot to impress these old bones, and while I’m all for new bikes, it seems that when the Milan show circus comes round, I find my gast is less and less flabbered every year. Luckily for my mojo, that wasn’t true at last winter’s showcase, and that’s mostly down to one bike – the new Panigale V4R. Okay, the carbon wings are pretty, and the new Öhlins NPX25/30 forks might please the suspension nerds, while much of the rest of it is familiar from the also-incredible Panigale V4S. It was one part of the spec sheet, however, that really smacked my gob, concerted my dis, and founded my dumb. It was the power output, and more specifically, the revs at which it made said power. A brain-frying 221bhp, at 15,250rpm. Yep, fifteen thousand, two hundred and fifty revs every minute. In road trim. The actual redline is even higher! The limiter kicks in at 16,000rpm in gears one-five, but in top gear (sixth), it gets another 500 revs, to 16,500rpm.
To put this in perspective, the 2008 Yamaha R6 exploded our heads with its peak power made at 14,500rpm. The legendary Honda CBR400RR NC29, launched 25 years ago, was a proper high-revver, and only hit 14,500rpm. You’ll have to go to the lunatic 250cc inline-four Japanese domestic market machinery of the early ‘90s to find a road bike that revs higher – the MC22 CBR250RR redlined at 19,000rpm, thanks to its teeny 33.8mm stroke. The CBR250 only made about 40bhp, though, and its pistons were more like tiny thimbles than the coffee cup-sized slugs in a litre superbike.
More revs, more power
So how does the Panigale V4R redline compare with its peers? Frankly, it makes them all look a bit weak. The other new litre bikes for this year are the BMW S1000RR and the revamped Kawasaki ZX-10R range. The Beemer peaks at 13,500rpm, with a 14k redline. Pfft. In the green corner, the new RR version of the ZX-10 Ninja has a special new valvetrain design aimed to raise revs by 600rpm, and now makes its peak power at 13,500rpm, with the rev limiter calling it quits at 14,800rpm. That’s good, but it’s still a hefty 1,700 revs shy of the V4R. So, the Panigale is the rev boss. But why are high revs such a good thing? Broadly speaking, revs literally mean power. The power output of an internal combustion engine is calculated by the force applied at the crank (or torque), multiplied by the rpm (the equation is pretty simple: power = torque x rpm / 7,120, using Nm for torque and bhp for power). So, when you look at a dyno chart, the power curve kinda follows the shape of the torque curve. If the torque’s steady, the power increases gradually as the revs climb, and any sudden spikes in the torque curve leads to a corresponding peak in the power curve.
But increasing the torque can only get you so far. In crude terms, torque is a measure of the force created at the piston top by the igniting the fuel/air mix. A bigger bang will, all things being equal, give a bigger shove to the piston. Imagine a Tour de France cyclist – give him a huge pair of thighs (say, by injecting him with horse steroids), and he’ll be able to shove harder on the pedals, pull higher gears, go up hills faster – make more power, in other words.
Performance at a price
If you’re limited by the amount of fuel and air burning in each cylinder, then there comes a point where you’ll hit the limits of the force produced on each combustion stroke. Improving efficiency is one way of making a bigger bang – make sure all the fuel burns efficiently, increasing the compression ratio, having a strong ignition system, ensuring the fuel/air mixture is exactly right. Fitting a turbocharger or increasing the cylinder bore also forces more fuel and air in, and makes for a bigger bang. If you can’t do this (as with a WSBK-homologated 999cc motor), then the only other way is to make the same size of bang, but at higher revs. Our massively-thighed cyclist could go even faster by pumping his giant legs even faster on the pedals. More revs – or pedal pushes – per minute, with the same force makes you go faster, since you’re making more power.
There are a few enemies of revs in an engine. As the rpm goes up, there is less and less time to get fuel/air into the cylinder, burn it, and get the exhaust gasses out. Even at a lowly 5,000rpm, a four-stroke engine fires nearly 42 times a second, and the piston moves up and down the bore four times as often, about 170 times a second. So, if the inlet valve is open for the whole of the piston inlet stroke, there’s just 1/170th of a second to get the whole fuel/air charge into the cylinder before the valve closes. At the redline of the new Panigale V4R (16,500rpm in top gear) there are 137.5 combustions per second, in each cylinder. And the piston makes the journey up and down the cylinder 550 times a second. So there’s 1/550th of a second to fill the cylinder with fuel and air.
Okay, air can be moved fast, and big ports and valves, large throttle bodies, carefully-sized inlet trumpets, cunning exhaust systems all help here. But there’s a downside here. Big ports and valves aren’t as good at low speeds, so what you gain up top you lose down low if you’re not careful. Having 220bhp at the top end of a race engine is no good if your competitors are making 50bhp more through the midrange as you’re pulling out of a hairpin bend. Just making an engine breathe efficiently at super-high revs is difficult enough, but the next enemy is a mechanical one – maximum piston speed. As aforementioned, at high revs the piston moves up and down the bore a lot. There comes a point where the speed gets so high, that normal aluminium can’t hold up any more. The forces on the rings, and the friction created by the high speed is bad enough, but you also need to cope with the massive forces at top and bottom dead centre, when the piston and rod have to be stopped, then started moving again in the other direction.
Maxing out
How fast does a piston move, then? There’s a fairly simple equation to work it out – average piston speed = 2 x stroke x (RPM/60). If you’ve got ten minutes to spare on Excel, you can work out the piston speeds for some engines, and you’ll quickly see the current limits. The 2019 S1000 RR makes peak power at 13,500rpm with a stroke of 49.7mm, and at that point its piston speed is 22.36m/s. At the redline of 14,600rpm, the little Bavarian pistons are whistling along at 24.18m/s. The V4S pistons move at 25.85m/s at its 14,500rpm redline, while the new V4R pushes this up to 26.62m/s at the 16,500rpm top-gear redline. Erk.
This explains why the Panigale V4R piston is such an advanced design. Ducati’s used a two-ring forged design rather than the three piston rings used on normal road engines (the only 4-stroke production bike on the market that goes down this route).
A three-ring design uses two compression rings and one oil scraper ring, but the V4R has just one compression ring and one oil ring to cut friction. It’s a bold step, and with one less ring, you might expect more in the way of oil consumption.
Ducati has lots of experience here, of course – its big twin superbikes had to make massive pistons move at big speeds – the 1299 Panigale’s soup-bowl pistons were hitting 25.6m/s at 11,500rpm. The 1199 Panigale R revved 500rpm higher: its pistons doing a stunning 26.72m/s at the 12,000rpm redline – the highest piston speed we can find on a ‘road’ bike. Therefore, making smaller pistons that can hold together at these speeds is well within the Bologna skill set. The final problem with high revs is the valves. While the crank spins once per engine revolution, the camshafts rotate twice as fast, and the valves have to open and close in a vanishingly small time period at high revs. As explained earlier, at 16,500rpm there’s 1/550th of a second for an intake and exhaust stroke, so the intake valves have to open fully, let the charge into the motor, then close again, sealing in massive combustion pressures. Then the exhaust valves have to open and let the red-hot gasses out in the same timespan. With conventional engine designs, the valve springs need to be very strong and stiff to bang the valves closed in time, which adds friction. There’s a big advantage in cutting weight here, of course, as lighter parts accelerate and decelerate much faster and the forces involved are smaller, so you can use lighter springs. Ducati uses titanium inlet valves and titanium valve retainer collets to cut mass, although the (smaller) exhaust valves are steel, because weight saving wasn’t worth the effort there.
Get the valve control wrong, and the valves can start to ‘float’ – staying open a fraction longer than desired, and that’s when the pistons can hit the valves and wreck the motor. Ducati has a advantage here, its desmodromic valve operation letting it use radical cam profiles, big valves, and high revs. Its engines use two cam profiles for each valve, one to open the valve and one to positively close it again. Using a mechanical cam to slam a valve closed rather than a spring means more exact valve movements, which is a massive benefit at high revs. So, in the end, maybe it’s not such a big surprise that Ducati is able to do this. It’s been working for years with massive piston speeds on its big-twin superbikes, and its decades of experience with desmodromic valves lets it apply that technology to the problem, too. Add in the closeness of the MotoGP Desmosedici engine design to the Panigale V4 motor, and perhaps we shouldn’t be so gobsmacked or dumbfounded at the V4R’s power and revs at all.